Úvod do karbidu kremíka
Karbid kremíka (SiC) je zložený polovodičový materiál zložený z uhlíka a kremíka, ktorý je jedným z ideálnych materiálov na výrobu vysokoteplotných, vysokofrekvenčných, vysokovýkonných a vysokonapäťových zariadení. V porovnaní s tradičným kremíkovým materiálom (Si) je pásmová medzera karbidu kremíka 3-krát väčšia ako u kremíka. Tepelná vodivosť je 4-5-krát väčšia ako u kremíka; prierazné napätie je 8-10-krát väčšie ako u kremíka; rýchlosť elektronického saturačného driftu je 2-3-krát väčšia ako u kremíka, čo spĺňa potreby moderného priemyslu pre vysoký výkon, vysoké napätie a vysokú frekvenciu. Používa sa hlavne na výrobu vysokorýchlostných, vysokofrekvenčných, vysokovýkonných a svetelne emitujúcich elektronických súčiastok. Medzi oblasti následného použitia patria inteligentné siete, vozidlá s novou energiou, fotovoltaická veterná energia, 5G komunikácia atď. Komerčne sa používajú karbidové diódy a MOSFETy z kremíka.
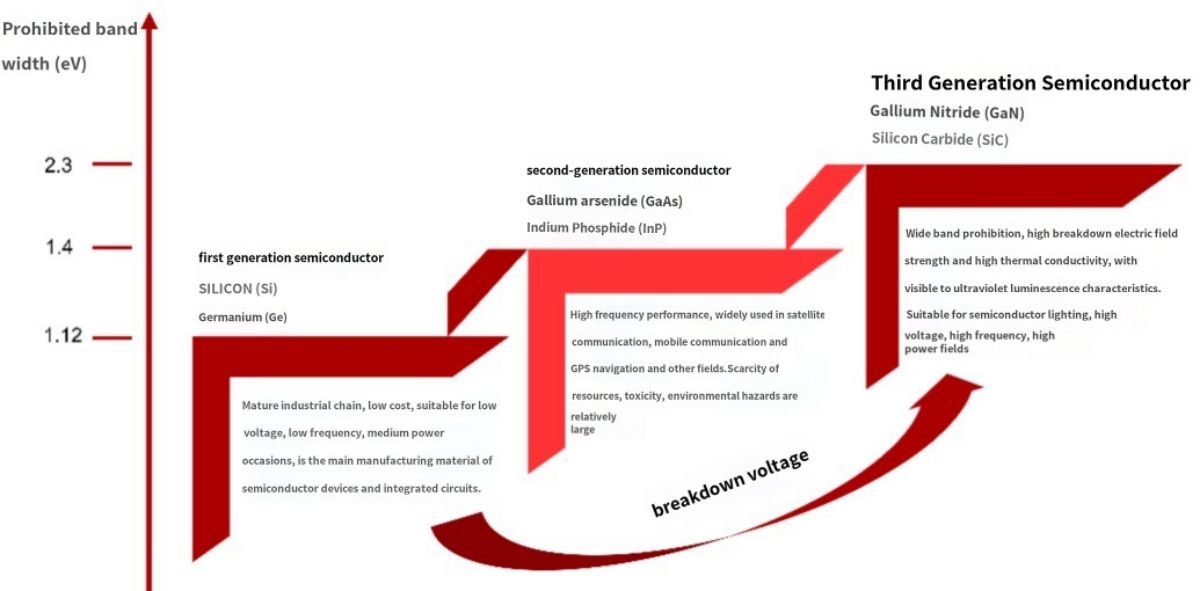
Odolnosť voči vysokým teplotám. Šírka pásmovej medzery karbidu kremíka je 2 až 3-krát väčšia ako u kremíka, elektróny pri vysokých teplotách ľahko neprechádzajú a odolávajú vyšším prevádzkovým teplotám. Tepelná vodivosť karbidu kremíka je 4 až 5-krát väčšia ako u kremíka, čo uľahčuje odvod tepla zariadením a zvyšuje prevádzkovú teplotu. Odolnosť voči vysokým teplotám môže výrazne zvýšiť hustotu výkonu a zároveň znížiť požiadavky na chladiaci systém, čím sa terminál stáva ľahším a menším.
Odoláva vysokému tlaku. Prierazná sila elektrického poľa karbidu kremíka je 10-krát väčšia ako u kremíka, ktorý odolá vyššiemu napätiu a je vhodnejší pre vysokonapäťové zariadenia.
Vysokofrekvenčný odpor. Karbid kremíka má dvojnásobnú rýchlosť driftu elektrónov v nasýtenom stave v porovnaní s kremíkom, čo vedie k absencii chvostového prúdu počas procesu vypínania, čo môže účinne zlepšiť frekvenciu spínania zariadenia a dosiahnuť miniaturizáciu zariadenia.
Nízke energetické straty. V porovnaní s kremíkovým materiálom má karbid kremíka veľmi nízky odpor v zapínaní a nízke straty v zapínaní. Zároveň veľká šírka pásmovej medzery karbidu kremíka výrazne znižuje zvodový prúd a straty výkonu. Okrem toho, karbid kremíka nemá počas procesu vypínania jav vlečného prúdu a straty pri prepínaní sú nízke.
Priemyselný reťazec z karbidu kremíka
Zahŕňa to najmä substrát, epitaxiu, návrh zariadenia, výrobu, utesnenie atď. Karbid kremíka z materiálu do polovodičového napájacieho zariadenia prechádza rastom monokryštálov, krájaním ingotov, epitaxným rastom, návrhom doštičky, výrobou, balením a ďalšími procesmi. Po syntéze prášku karbidu kremíka sa najprv vyrobí ingot z karbidu kremíka, potom sa krájaním, brúsením a leštením získa substrát z karbidu kremíka a epitaxným rastom sa získa epitaxná vrstva. Epitaxná doštička sa vyrába z karbidu kremíka litografiou, leptaním, iónovou implantáciou, pasiváciou kovu a ďalšími procesmi, doštička sa nareže na matricu, zariadenie sa zabalí a zariadenie sa spojí do špeciálneho plášťa a zostaví sa do modulu.
Predchádzajúci priemyselný reťazec 1: substrát - rast kryštálov je kľúčovým procesným článkom
Substrát z karbidu kremíka predstavuje približne 47 % nákladov na zariadenia z karbidu kremíka, čo predstavuje najvyššie technické bariéry výroby a najväčšiu hodnotu a je jadrom budúcej rozsiahlej industrializácie SiC.
Z hľadiska rozdielov v elektrochemických vlastnostiach možno materiály substrátov z karbidu kremíka rozdeliť na vodivé substráty (oblasť rezistivity 15 ~ 30 mΩ·cm) a poloizolované substráty (rezistivita vyššia ako 105 Ω·cm). Tieto dva druhy substrátov sa používajú na výrobu diskrétnych zariadení, ako sú výkonové zariadenia a rádiofrekvenčné zariadenia, po epitaxnom raste. Poloizolovaný substrát z karbidu kremíka sa používa hlavne pri výrobe RF zariadení z nitridu gália, fotoelektrických zariadení atď. Pestovaním epitaxnej vrstvy gan na poloizolovanom substráte SIC sa pripraví epitaxná doska sic, ktorú je možné ďalej spracovať na HEMT gan izonitridové RF zariadenia. Vodivý substrát z karbidu kremíka sa používa hlavne pri výrobe výkonových zariadení. Na rozdiel od tradičného výrobného procesu kremíkových napájacích zariadení nie je možné napájacie zariadenie z karbidu kremíka vyrobiť priamo na substráte z karbidu kremíka. Na získanie epitaxnej vrstvy z karbidu kremíka je potrebné naniesť epitaxnú vrstvu z karbidu kremíka na vodivý substrát a epitaxná vrstva sa vyrába na Schottkyho dióde, MOSFETe, IGBT a iných napájacích zariadeniach.
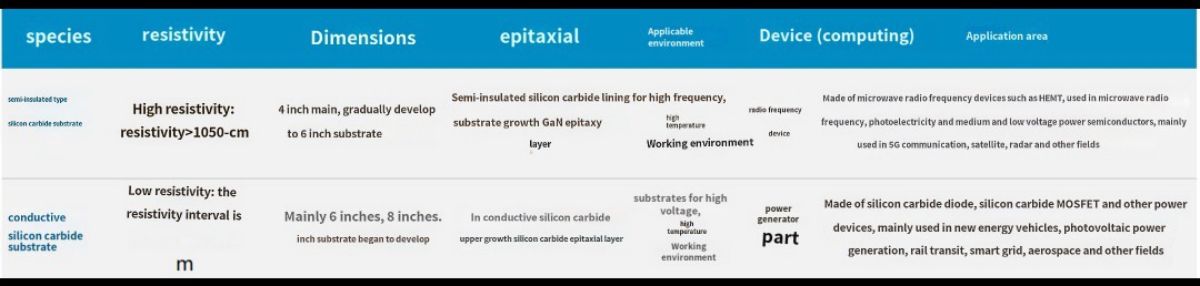
Prášok karbidu kremíka bol syntetizovaný z vysoko čistého uhlíkového prášku a vysoko čistého kremíkového prášku a rôzne veľkosti ingotov karbidu kremíka boli pestované v špeciálnom teplotnom poli a potom bol substrát z karbidu kremíka vyrobený prostredníctvom viacerých procesov spracovania. Základný proces zahŕňa:
Syntéza surovín: Vysoko čistý kremíkový prášok a toner sa zmiešajú podľa receptúry a reakcia sa vykonáva v reakčnej komore pri vysokej teplote nad 2000 °C, aby sa syntetizovali častice karbidu kremíka so špecifickým typom kryštálov a veľkosťou častíc. Následne sa častice drvením, triedením, čistením a ďalšími procesmi spĺňajú požiadavky na vysoko čistý karbid kremíka ako surovinu.
Rast kryštálov je základným procesom výroby substrátu z karbidu kremíka, ktorý určuje elektrické vlastnosti substrátu z karbidu kremíka. V súčasnosti sú hlavnými metódami rastu kryštálov fyzikálny prenos pár (PVT), vysokoteplotná chemická depozícia z pár (HT-CVD) a epitaxia v kvapalnej fáze (LPE). Spomedzi nich je metóda PVT v súčasnosti hlavnou metódou komerčného rastu substrátu SiC s najvyššou technickou vyspelosťou a najrozšírenejším používaním v strojárstve.
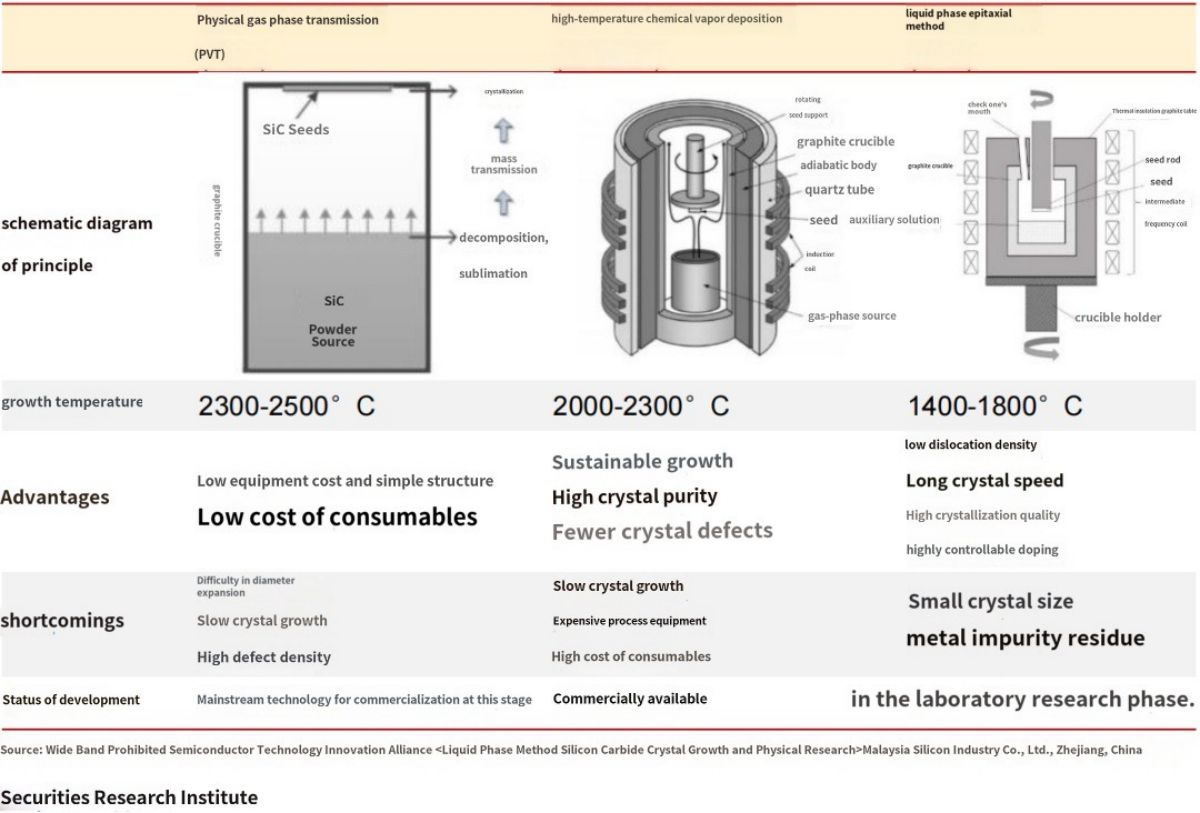
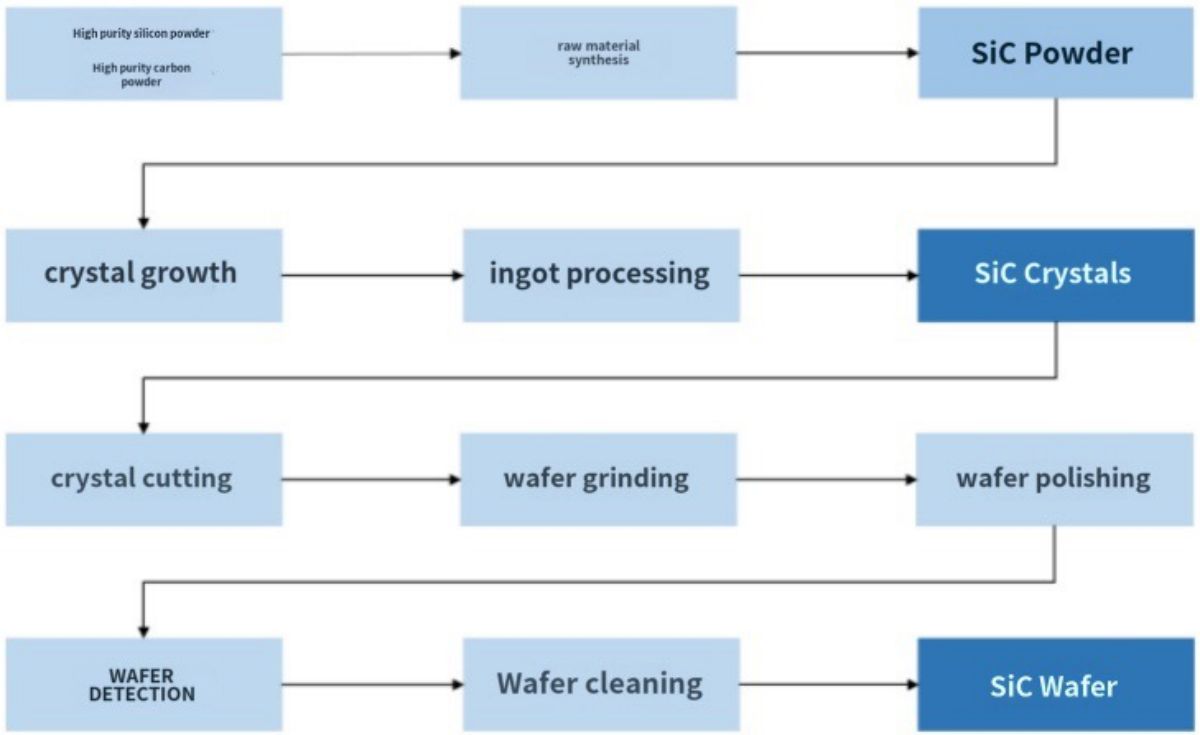
Príprava SiC substrátu je náročná, čo vedie k jeho vysokej cene.
Riadenie teplotného poľa je náročné: rast kryštálov Si vyžaduje iba 1500 ℃, zatiaľ čo kryštály SiC sa musia pestovať pri vysokej teplote nad 2000 ℃ a existuje viac ako 250 izomérov SiC, ale hlavná monokryštalická štruktúra 4H-SiC na výrobu výkonových zariadení, ak nie je presne riadená, získa iné kryštálové štruktúry. Okrem toho teplotný gradient v tégliku určuje rýchlosť sublimačného prenosu SiC a usporiadanie a spôsob rastu plynných atómov na kryštalickom rozhraní, čo ovplyvňuje rýchlosť rastu kryštálov a kvalitu kryštálov, takže je potrebné vytvoriť systematickú technológiu riadenia teplotného poľa. V porovnaní s materiálmi Si spočíva rozdiel pri výrobe SiC aj vo vysokoteplotných procesoch, ako je vysokoteplotná iónová implantácia, vysokoteplotná oxidácia, vysokoteplotná aktivácia a proces tvrdej masky, ktorý si tieto vysokoteplotné procesy vyžadujú.
Pomalý rast kryštálov: rýchlosť rastu kryštálov Si môže dosiahnuť 30 ~ 150 mm/h a výroba 1-3 m kryštálovej tyče z kremíka trvá iba približne 1 deň; napríklad kryštálová tyč SiC vyrobená metódou PVT má rýchlosť rastu približne 0,2-0,4 mm/h, pričom 7 dní trvá rast menej ako 3-6 cm, čo predstavuje rýchlosť rastu menej ako 1% kremíkového materiálu a výrobná kapacita je extrémne obmedzená.
Vysoké parametre produktu a nízky výťažok: medzi základné parametre substrátu SiC patrí hustota mikrotubulov, hustota dislokácií, odpor, deformácia, drsnosť povrchu atď. Usporiadanie atómov v uzavretej vysokoteplotnej komore a dokončenie rastu kryštálov pri súčasnom riadení indexov parametrov je zložité systémové inžinierstvo.
Materiál má vysokú tvrdosť, vysokú krehkosť, dlhý čas rezania a vysoké opotrebenie: Mohsova tvrdosť SiC 9,25 je druhá hneď po diamante, čo vedie k výraznému zvýšeniu náročnosti rezania, brúsenia a leštenia a narezanie 35 – 40 kusov ingotu s hrúbkou 3 cm trvá približne 120 hodín. Okrem toho, kvôli vysokej krehkosti SiC, opotrebenie pri spracovaní doštičiek bude väčšie a výstupný pomer bude len okolo 60 %.
Trend vývoja: Zväčšenie veľkosti + pokles ceny
Globálny trh s 6-palcovými objemovými výrobnými linkami SiC dozrieva a popredné spoločnosti vstúpili na trh s 8-palcovými doskami. Domáce vývojové projekty sú prevažne 6-palcové. V súčasnosti, hoci väčšina domácich spoločností stále pracuje na 4-palcových výrobných linkách, priemysel sa postupne rozširuje na 6-palcové. S rozvojom technológie podporných zariadení pre 6-palcové dosky sa postupne zlepšuje aj domáca technológia SiC substrátov, čo sa prejaví aj v úsporách z rozsahu veľkých výrobných liniek a súčasný časový rozdiel medzi domácou hromadnou výrobou 6-palcových dosiek sa zúžil na 7 rokov. Väčšia veľkosť doštičky môže viesť k zvýšeniu počtu jednotlivých čipov, zlepšeniu výťažnosti a zníženiu podielu hranových čipov, pričom náklady na výskum a vývoj a strata výťažnosti sa udržia na úrovni približne 7 %, čím sa zlepší využitie doštičiek.
V návrhu zariadení stále existuje veľa problémov
Komercializácia SiC diód sa postupne zlepšuje a v súčasnosti niekoľko domácich výrobcov navrhlo produkty SiC SBD. Produkty SiC SBD pre stredné a vysoké napätie majú dobrú stabilitu. V palubnom riadení vozidla sa pomocou SiC SBD+SI IGBT dosahuje stabilná prúdová hustota. V súčasnosti neexistujú žiadne prekážky v patentovom dizajne produktov SiC SBD v Číne a rozdiel medzi nimi a zahraničím je malý.
SiC MOS stále čelí mnohým ťažkostiam, stále existuje priepasť medzi SiC MOS a zahraničnými výrobcami a príslušná výrobná platforma je stále vo výstavbe. V súčasnosti spoločnosti ST, Infineon, Rohm a ďalšie 600-1700V SiC MOS dosiahli masovú výrobu a podpísali a dodávajú zmluvy s mnohými výrobnými odvetviami, zatiaľ čo súčasný domáci návrh SiC MOS je v podstate dokončený, niekoľko výrobcov spolupracuje s továrňami vo fáze toku doštičiek a neskoršie overenie zákazníkmi si stále vyžaduje určitý čas, takže do rozsiahlej komercializácie je ešte dlhá doba.
V súčasnosti je planárna štruktúra hlavnou voľbou a v budúcnosti sa vo vysokotlakovej oblasti široko používa typ s výkopom. Výrobcov planárnych SiC MOS tranzistorov je veľa, planárna štruktúra v porovnaní s drážkou nespôsobuje lokálne poruchy, čo ovplyvňuje stabilitu prevádzky. Na trhu pod 1200 V má široké spektrum uplatnenia a planárna štruktúra je relatívne jednoduchá z hľadiska výroby, čo spĺňa dva aspekty výroby a kontroly nákladov. Drážkové zariadenie má výhody extrémne nízkej parazitnej indukčnosti, rýchlej spínacej rýchlosti, nízkych strát a relatívne vysokého výkonu.
2 – Novinky o SiC doštičkách
Rast produkcie a predaja na trhu s karbidom kremíka, venujte pozornosť štrukturálnej nerovnováhe medzi ponukou a dopytom
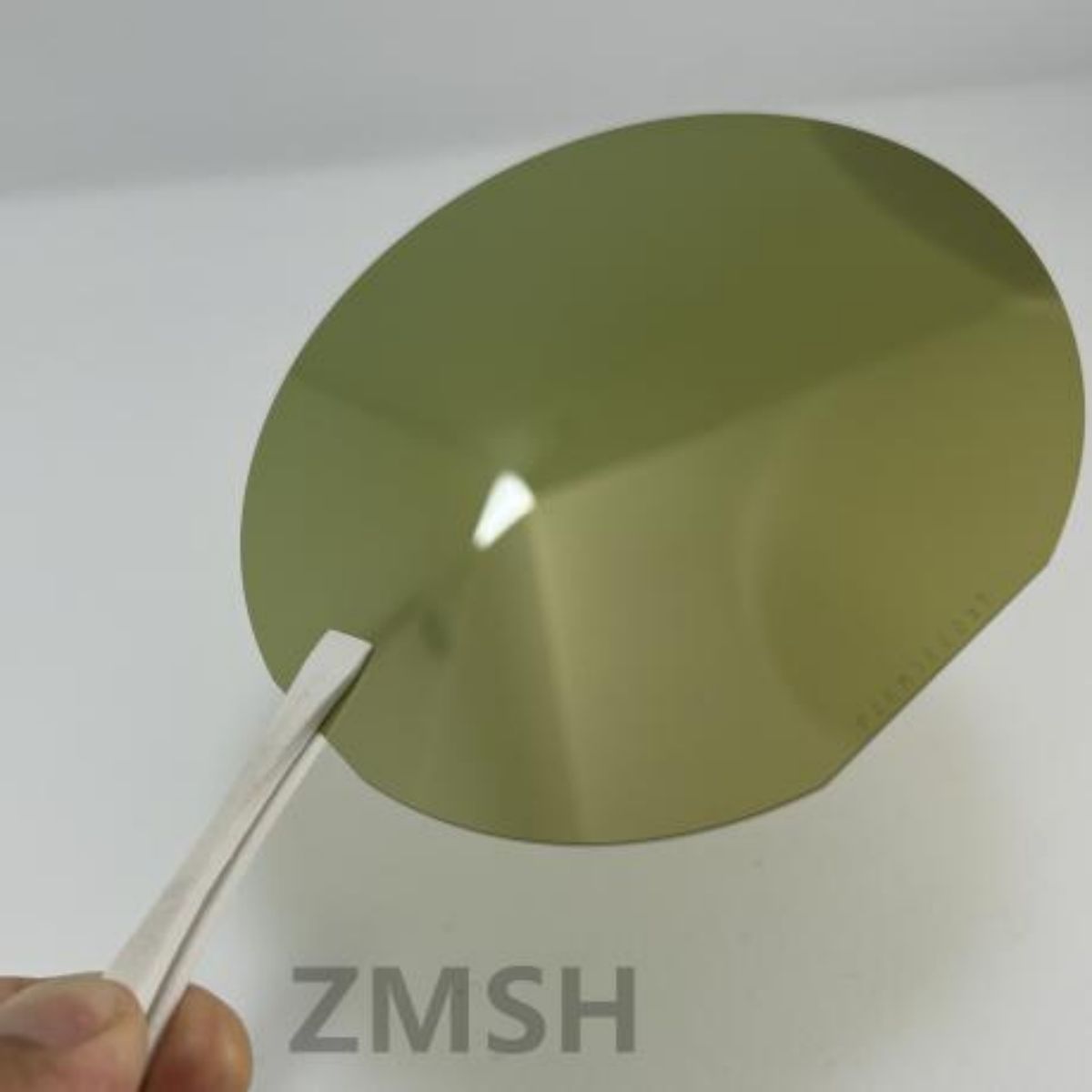
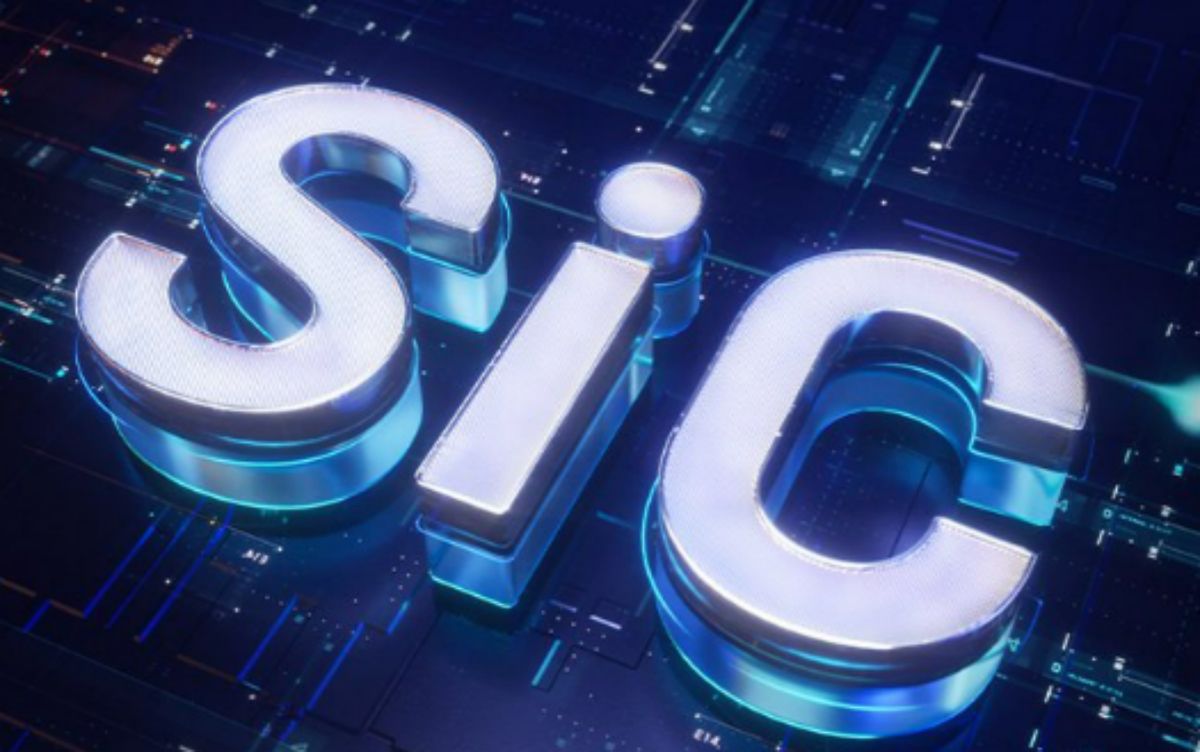
S rýchlym rastom dopytu na trhu po vysokofrekvenčnej a vysokovýkonnej výkonovej elektronike sa postupne prejavuje fyzikálne obmedzenie polovodičových súčiastok na báze kremíka a polovodičové materiály tretej generácie, ktoré predstavuje karbid kremíka (SiC), sa postupne industrializujú. Z hľadiska materiálových vlastností má karbid kremíka 3-krát väčšiu šírku pásmovej medzery ako kremíkový materiál, 10-krát väčšiu kritickú silu elektrického poľa a 3-krát väčšiu tepelnú vodivosť, takže výkonové súčiastky z karbidu kremíka sú vhodné pre vysokofrekvenčné, vysokotlakové, vysokoteplotné a iné aplikácie, ktoré pomáhajú zlepšiť účinnosť a hustotu výkonu výkonových elektronických systémov.
V súčasnosti sa na trhu postupne objavujú SiC diódy a SiC MOSFETy a existujú aj vyspelejšie produkty, medzi ktorými sa SiC diódy v niektorých oblastiach široko používajú namiesto kremíkových diód, pretože nemajú výhodu reverzného nabíjania; SiC MOSFET sa postupne používa aj v automobilovom priemysle, skladovaní energie, nabíjaní batérií, fotovoltaike a ďalších oblastiach; v oblasti automobilových aplikácií sa čoraz viac prejavuje trend modularizácie a na dosiahnutie vynikajúceho výkonu SiC je potrebné spoliehať sa na pokročilé procesy balenia. Technicky je relatívne vyspelé tesnenie plášťa ako hlavný prúd, čo je v budúcnosti vhodné pre vývoj plastových tesnení, ktoré sú prispôsobené vývojovým vlastnostiam SiC modulov.
Rýchlosť poklesu ceny karbidu kremíka alebo niečo, čo je nad rámec predstavivosti
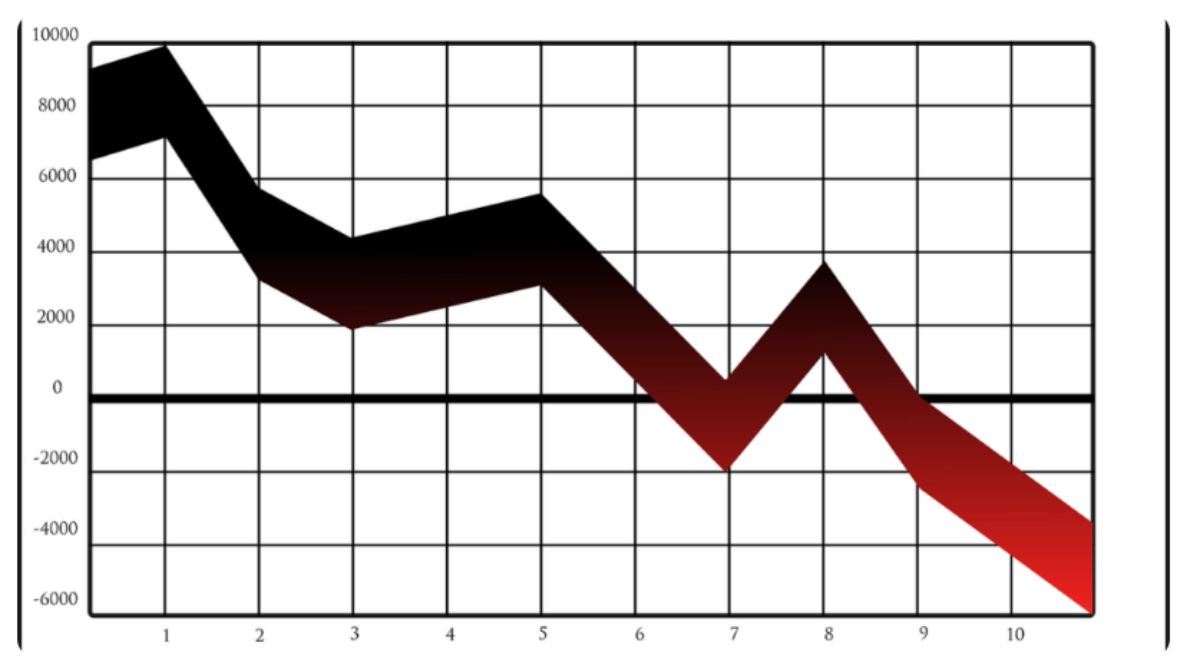
Použitie zariadení z karbidu kremíka je obmedzené najmä vysokými nákladmi. Cena SiC MOSFET na rovnakej úrovni je štyrikrát vyššia ako cena Si IGBT. Je to preto, že proces výroby karbidu kremíka je zložitý a rast monokryštálov a epitaxiálnych štruktúr nie je len negatívny pre životné prostredie, ale aj pomalý. Spracovanie monokryštálov do substrátu musí prejsť procesom rezania a leštenia. Vzhľadom na vlastnosti materiálu a nezrelú technológiu spracovania je výťažnosť domáceho substrátu menšia ako 50 % a rôzne faktory vedú k vysokým cenám substrátov a epitaxiálnych štruktúr.
Zloženie nákladov na zariadenia z karbidu kremíka a zariadenia na báze kremíka je však diametrálne odlišné, náklady na substrát a epitaxiu predného kanála predstavujú 47 % a 23 % z celkového zariadenia, čo predstavuje spolu približne 70 %, návrh zariadenia, výroba a tesniace články zadného kanála predstavujú iba 30 %, výrobné náklady na zariadenia na báze kremíka sú sústredené hlavne na výrobu doštičiek zadného kanála, približne 50 %, a náklady na substrát predstavujú iba 7 %. Fenomén hodnoty reťazca priemyslu karbidu kremíka hore nohami znamená, že výrobcovia epitaxie substrátov v predstihu majú základné právo hovoriť, čo je kľúčom k usporiadaniu domácich a zahraničných podnikov.
Z dynamického hľadiska na trhu, zníženie nákladov na karbid kremíka, okrem zlepšenia dlhých kryštálov karbidu kremíka a procesu rezania, vedie aj k rozšíreniu veľkosti doštičiek, čo je v minulosti aj zrelá cesta vývoja polovodičov. Údaje spoločnosti Wolfspeed ukazujú, že vylepšením substrátu karbidu kremíka zo 6 palcov na 8 palcov sa môže zvýšiť produkcia kvalifikovaných čipov o 80 % až 90 % a zlepšiť výťažnosť. To môže znížiť kombinované jednotkové náklady o 50 %.
Rok 2023 je známy ako „prvý rok 8-palcového SiC“. V tomto roku domáci a zahraniční výrobcovia karbidu kremíka zrýchľujú plánovanie 8-palcového karbidu kremíka. Napríklad spoločnosť Wolfspeed investovala 14,55 miliardy amerických dolárov do rozšírenia výroby karbidu kremíka, ktorého dôležitou súčasťou je výstavba závodu na výrobu 8-palcových substrátov SiC. S cieľom zabezpečiť budúce dodávky 200 mm holého kovu SiC pre viacero spoločností podpísali spoločnosti Domestic Tianyue Advanced a Tianke Heda dlhodobé zmluvy so spoločnosťou Infineon na dodávky 8-palcových substrátov z karbidu kremíka v budúcnosti.
Podľa údajov z výskumu spoločnosti Ji Bond Consulting sa od tohto roku zrýchli nárast výroby karbidu kremíka zo 6 palcov na 8 palcov. Spoločnosť Wolfspeed očakáva, že do roku 2024 sa jednotková cena čipu pre 8-palcový substrát v porovnaní s jednotkovou cenou čipu pre 6-palcový substrát v roku 2022 zníži o viac ako 60 % a tento pokles nákladov ďalej otvorí trh s aplikáciami. Súčasný podiel 8-palcových produktov na trhu je menej ako 2 % a očakáva sa, že do roku 2026 vzrastie na približne 15 %.
V skutočnosti tempo poklesu ceny substrátu z karbidu kremíka môže presiahnuť predstavy mnohých ľudí. Súčasná trhová ponuka 6-palcového substrátu je 4 000 – 5 000 juanov/kus, čo v porovnaní so začiatkom roka výrazne kleslo a očakáva sa, že v budúcom roku klesne pod 4 000 juanov. Stojí za zmienku, že niektorí výrobcovia, aby získali prvé miesto na trhu, znížili predajnú cenu na nižšiu úroveň nákladov. Spustil sa model cenovej vojny, ktorý sa sústredil najmä na ponuku substrátu z karbidu kremíka v oblasti nízkeho napätia. Domáci aj zahraniční výrobcovia agresívne rozširujú výrobné kapacity alebo skôr dovoľujú, aby sa ponuka substrátu z karbidu kremíka dostala do štádia prebytku, ako si predstavovali.
Čas uverejnenia: 19. januára 2024